What are industrial robots? What are their types?
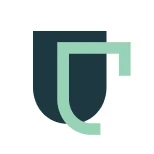
Franco Brutti
Did you know that, according to Zippia, there are already more than 3 million industrial robots worldwide, and that the number is expected to multiply by 2030?
Industrial robots are at the forefront of industrial development and already play a crucial role in the production chains and supply lines of thousands of companies.
Robots are the main focus of countless new technological advances. And for some, they are leading the fourth industrial revolution we are living in today. Knowing about these robots is therefore vital, both for professionals and business owners.
Interested in finding out which robots are at the forefront of the development of industrial robotics? Then you're in the right place. Here we will tell you all about these robots and their different applications:
What are industrial robots?
Exactly that, machines are designed to multiply production and efficiency in various types of industrial tasks, especially in manufacturing and production areas.
Industrial robots are programmable, making them the right tools to automate a huge range of operations, including welding, assembly and material handling, among many other applications.
These robots are designed for industrial environments, including factories, production plants and production lines.
They are perfect for streamlining the operation of any company's industrial apparatus, minimizing long-term costs and preventing accidents in hazardous tasks and environments.
In addition, they can handle repetitive, high-precision tasks with more efficiency and better reach than non-automated machinery. And they can minimize the workload of industrial operators.
Characteristics of industrial robots
Let's see the most important features and parts of these robots:
Articulated mechanical arm: perhaps the most characteristic part of industrial robots - and the most important. It has a series of articulated segments, joints, links, transmissions and one or more heads.
Controller: or rather, the brain of the robot, the computer in charge of processing instructions and coordinating movements and making adjustments to perform its tasks. In addition, thanks to the controller, the robot can connect and communicate with other systems.
Sensors: the equivalent of the robot's nervous system. It has encoders and other tools to guide the robotic arm and tell the controller what task or adjustment to perform.
End-effectors: such as grippers, laser heads and any tools or devices that can be added to the arm for specific tasks.
Vision systems: cameras, photocells and image processing systems, facial recognition and other vision applications.
These are the essential parts that the vast majority of robots for industry possess. However, there is a huge variety of tools and accessories to complement each of these sections.
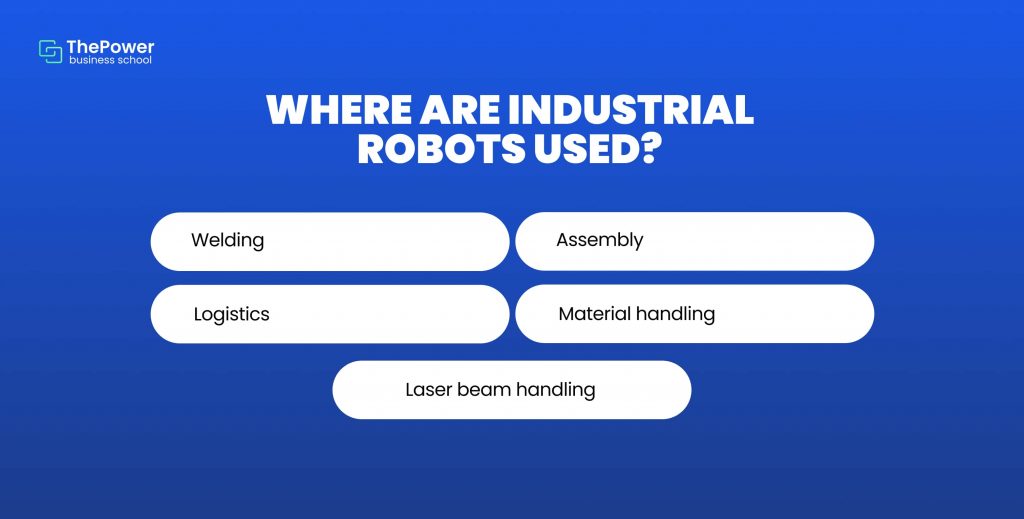
Where are industrial robots used?
Although industrial robotics is applicable in countless sectors, these are the preferred areas for these robots:
Welding: industrial robots are more than indispensable in this area, whether for MIG welding, TIG welding or spot welding. They are therefore essential for the manufacture of countless products.
Assembly: industrial robots are key in the entire production cycle but especially in assembly. Thanks to their mechanical arms, sensors and vision systems, they can assemble components with greater speed, consistency and quality.
Logistics: especially for warehousing, loading, unloading and internal transportation. It also plays a crucial role in product packaging, both for picking and choosing the items to be packaged and for packing and labeling them.
Material handling: from industrial materials to potentially lethal chemicals and toxic substances. Also for working in high temperatures (such as in foundries), as well as in adverse conditions.
Laser beam handling: for several of the above tasks, as well as for laser marking and engraving, heat treatment and laser cleaning, among other tasks.
The 6+1 types of industrial robots
Now that we know their different characteristics and areas of application, let's take a look at a classification list of industrial robots.
1. Cartesian robot
The Cartesian robot is one of the most commonly used in industry and robotics. It moves along three Cartesian axes (X, Y, Z), through motors and belts. However, they can have up to 6 perpendicular sliding axes.
In addition, they are equipped with sensors and cameras to measure distances, detect and identify objects.
These robots can be used for small tasks, such as micro-manufacturing and micro-assembly in electronics. Also for large-scale tasks, such as automotive assembly and steel handling.
They have a high payload capacity, so they can handle large objects. In addition, they’re quite accurate for tasks requiring linear movements and can move at high speed in a straight line.
Advantages:
Fairly accurate for component placement.
Ability to handle heavy loads and bulky objects.
Fast movements in straight lines within its three axes.
Disadvantages:
Can only move in straight lines in the X, Y and Z axes.
They take up a lot of physical space, not to mention the space they require to move.
Applications:
Microelectronics.
Assembly automation.
3D printing.
Packaging and wrapping.
Material handling.
Food and pharmaceutical handling.
2. Cylindrical robot
This robot is characterized by its rotating joint, as well as its prismatic joint for movement.
Thanks to its axis of rotation, it can rotate its robotic arm through 360 degrees. Thus, it can execute circular and linear movements in a horizontal plane. In addition, it’s able to retract vertically and rotate around this same axis.
However, it’s designed to work in a static environment. In other words, it cannot move on its own.
Its static design gives it more stability and rigidity, which gives it a huge payload capacity compared to other industrial robots.
Advantages:
Fairly fast and accurate in horizontal planes.
More compact than other robots (depending on its size).
Greater stability and structural rigidity to handle heavy loads.
Disadvantages:
As a static robot, it cannot move on its own.
Limited working area, mainly due to its extended vertical arm.
Cannot move in vertical planes, only horizontally.
Applications:
Welding line automation.
Assembly lines.
Coating.
Material handling.
Heavy load handling.
Warehousing.
Wrapping and packaging.
3. Delta robot
The delta robot is easy to recognize thanks to its delta shape, that is, its triangular shape. It has an inverted triangle structure. It’s composed of a mobile platform and three articulated arms, connected by spherical joints.
Like the Cartesian robot, the arms of this robot can move in X, Y, Z axes. However, they are the right alternative for working in vertical planes.
They are also more flexible and can cover a larger working area. Unlike the previous two robots, they are more focused on performing precise tasks rather than load handling.
Advantages:
High speed and accuracy for fast cycle applications.
Long reach in the vertical plane.
Can be used in different environments.
They do not take up more space than they need.
Disadvantages:
Cannot deal with a lot of payload.
Cannot move on its own.
Only works in vertical planes.
They are not the right choice for material handling.
Applications:
Microelectronics.
Microassembly.
Micro welding.
Food and pharmaceutical handling and packaging.
Product selection and sorting.
Printing and painting.
4. SCARA Robot
The SCARA robot (Selective Compliance Assembly Robot Arm) is perfect for a number of industrial robotics applications.
It has an articulated arm and rotating joints on horizontal axes. It’s perfect for executing fast and fairly precise movements in horizontal planes. It can also work in vertical planes, although its capacity is much more limited.
It’s possibly the most suitable robot for pick & place tasks, depending on the payload to be handled.
In addition, this robot is widely used in the medical industry for a variety of tasks. And it has even been tested in assisted surgeries.
Advantages:
High precision and longer reach in the horizontal plane.
Small and compact working space.
Adaptable to different environments and specific areas.
Perfect for repetitive, high-speed tasks.
Disadvantages:
Limited movement in vertical planes.
Requires complex configurations.
Cannot handle large payloads.
Applications:
Component assembly.
Printed circuit board placement.
Quality testing.
Packing and packaging.
Material handling.
In the medical industry:
Sample handling.
Packaging, packing and labeling.
Pipetting.
Solution preparation.
Laboratory automation.
Processing and packaging.
Assisted surgeries.
5. Spherical robot or polar robot
The polar robot is one of the most versatile among industrial robots. It can be used both in production lines and in the research and development of robotics, artificial intelligence and biomechanics.
And it can also be used in the medical industry for product manufacturing and assisted surgeries.
This robot has a fixed base with three degrees of freedom, that is, the three X, Y and Z axes. In addition, it has an extendable articulated arm that can move in different directions and rotate in multiple axes.
In other words, this robot can move in different directions and operate in three-dimensional planes; that is, it can work in horizontal and vertical planes and has a great capacity for movement, and can even work in inclined positions.
This robot is more compact, which gives it better access to difficult environments and spaces, not to mention that it has a great deal of freedom of movement in such spaces. And in addition, some models can be controlled remotely and even operate autonomously.
Advantages:
Ability to work in three-dimensional spaces.
It can execute movements in different horizontal planes.
It can also work in diagonal positions and inclined angles.
Takes up less space due to its compact size.
Disadvantages:
Lower payload capacity.
Higher programming complexity.
Some models can be quite expensive and difficult to develop.
Applications:
Assembly.
Fabrication.
Welding.
Inspection and quality control.
Prototyping.
Research and development.
Assisted surgeries.
Biomechanics.
Underwater exploration.
Planetary exploration.
6. Collaborative robot or co-bot
This definition covers all types of robot models. However, collaborative robots are designed to work directly with humans in industrial environments.
These robots have several tools to interact safely with operators. For example, they have more intuitive human-machine interfaces, touch screens and simple controllers, among other features. Not to mention that they are easier to program.
They also have advanced sensors, such as proximity, force and vision sensors to identify and respond to human presence. And they are designed to prevent accidents and minimize risks in industrial environments.
Advantages:
They ensure safe collaboration.
Prevent injuries, accidents and occupational hazards.
Easy to program and operate.
Adaptable to different types of work and industrial environments.
Easy to integrate into all types of industrial processes.
Disadvantages:
Their initial cost is among the highest in the market.
For safety reasons, they are usually slower than other robots.
They have less maximum load capacity.
Applications:
Inspection and quality control.
Assembly.
Welding.
Handling and joining of components.
Palletizing.
Electronic assembly.
Handling of fragile objects.
6+1. Autonomous Robot (AMR)
This robot is one of the most valued in industrial robotics due to its ability to operate on its own, with less human intervention.
It comes in a variety of sizes and models. Although similar to collaborative robots, these are intended to work autonomously. That is, they can make decisions and perform actions without human supervision.
Collaborative robots, on the other hand, are designed to coordinate directly with their operators.
This robot has advanced data processing systems to perceive the environment and identify the human being.
In addition, it has actuators to control its own movements and feedback and adjustment systems to adapt to its environment. However, since it’s designed to work on its own, it has fewer safety mechanisms.
Advantages:
Reduces long-term costs.
Adaptable to different tasks and environments.
Designed for hazardous environments.
It has an automatic learning system.
Greater accuracy and consistency.
Disadvantages:
Requires more training time.
More difficult to program and configure.
Limited decisions in unforeseen or unpredictable situations.
Less interactive than collaborative robots.
Applications:
Assembly.
Welding.
Material handling.
Palletizing.
Production line automation.
Product delivery.
Space and underwater exploration.
Industrial robots have already revolutionized manufacturing, production and logistics lines in thousands of companies and represent the future of robotics in countless industries.
If you want to be three steps ahead in your industry, whether you are a student, professional or run your own company, these robots are essential to get there.
And now, tell us.
Did you already know any of these robots? What other applications do you think they could have? We look forward to your comments.
Looking for something specific?