What is lean management and why should you know about it?
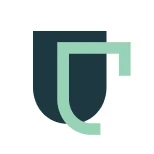
Franco Brutti
You have a lot of losses in your business and you don't know how to solve this problem? We bring you the solution: lean management.
It's a methodology of work based on continuous improvement. As the saying goes: "Little by little until the objectives are achieved". With lean management, the aim is precisely to make small changes that in the long term will have a positive impact on the organisation.
Forget about wasted resources, idle departments and unproductive staff. It's time to create a new organisational culture and with lean management you will get it.
Shall we start now?
What is lean management?
Let's start by defining lean management. It's one of today's most modern management systems and it focuses exclusively on the customer. The idea is to address all the complexities of the marketplace to improve every single business process.
In other words, it is the process that seeks to eliminate all the waste of resources in a company to achieve concrete results in the shortest possible time. This way, important problems are eliminated, such as:
1. Waste of time
With this methodology, a precise study is made of each of the business processes and it is determined how they can be executed in the shortest possible time. The idea is to reduce the waiting and manufacturing time of the product so that the customer is satisfied at all times.
2. Unnecessary effort
As well as seeking to be more efficient, we eliminate those processes that definitely don't make sense at present. To achieve this, every single action is studied to determine what can and cannot continue.
3. Expense control
Simple, all expenses that are not related to an increase in productivity or profit will be eliminated. This will give you more liquidity to make new investments.

When did lean management start?
Never heard of the term lean management? Well, you should know that it has been around for more than 50 years, as it was first mentioned after the Second World War when Toyota had to implement major changes to stay in the market.
In this regard, priority was given to spending money only on what would sell. Therefore, the company's entire production capacity was adjusted to the demand and a process standard was implemented to ensure product quality
Steps to implement lean management in your company
There are several steps to follow to implement lean management in your company. The most important thing is to change the mindset of the organisation to fundamentally change the behaviours that have brought them to this point.
The good news is that it works for both large and small companies, so you have no excuse not to implement it in your business. Let's take a look at the steps to successfully implement it below:
Step 1: Start the process
Many specialists indicate that the most difficult step is to start the process, so the best thing you can do is not overthink it and start with what you have.
Although it might seem strange, it's more common than you think. It's about moving against the tide and breaking the inertia that has existed in the organisation for many years, i.e. getting out of the comfort zone.
It's important that someone has knowledge of the lean method and finds some kind of leverage to start making all the changes that are necessary.
Step 2: Study the processes and the product
In this second stage, it's essential to carry out a detailed study of each of the processes and products that are currently being made in the company.
To do this, it's best to assemble a team that will allow you to gather data, statistics and graphs to see with real numbers which points can be optimised in the short and medium term.
Step 3: Plan the improvement
OK, once you have the research in hand it's time to map out what the objectives of implementing lean management are. This can range from improvements in effort, time or reduction of fixed costs to investing in new projects.
It's important at this stage to take into account what human and financial capital the organisation has and what the chain of command is like in order to make the necessary improvements.
Step 4: Carrying out the plan
The moment of truth has arrived. This is where all the improvements that were planned at the beginning are implemented to take the company to the next level.
It's a good idea to start with IT processes and then move on to business resources and staff training.
At the same time, it's advisable to apply different lean techniques to increase the chances of success. You can use the 5S method: sort, set in order, shine, standardise and sustain.
Step 5: Monitoring
Once the best ones are implemented, it's important to constantly monitor whether you are achieving the results you expected at the beginning of the process.
It's important to remember that lean management is based on continuous improvement, so every action you implement should be analysed immediately. This way you will detect problems before it's too late.
The good news is that nowadays there are tools like Kanban boards to evaluate everything in real time.

5 Advantages of lean management
There are many advantages of lean management for a company. It's true that sometimes you have to touch as few buttons as possible to keep the company running smoothly, but there are times when you have to take risks to achieve better results.
Take a look at some of these advantages:
1. Much more efficient production
And we couldn't start any other way. One of the biggest problems companies have is the waste of both human and financial resources, which puts them at a disadvantage compared to the competition.
Often there are employees and positions that are unnecessary. This requires money for payroll, taxes and fixed costs that can be reduced with lean management.
2. Employee efficiency
Imagine spending time on tasks and processes that add no value to the business. This translates into millions of dollars in losses for the company if you think about it in the long run, so it's time to change the situation completely.
Now with lean management you will use those resources on tasks that do bring numbers into the equation. You will see how that money will go into making products that in a short time will make you a profit.
This way, human capital will have clear guidelines on what to do and how to do it to achieve the goals that were set at the beginning of the process.
3. Reduction of losses due to unproductive processes
By controlling the entire production process, losses of money in processes that definitely do not make sense for the company are reduced.
Many companies fall down because they fail to detect those ant-like expenses that in the long run turn into gigantic expenses that end up bankrupting them. Forget about this problem and optimise your budget to the maximum.
4. Inventory control
Inventory control is a delicate part of the whole business process. When a product is manufactured, losses are generated by bad practices, system failures and the use of obsolete raw materials.
Therefore, if you apply lean management you will detect if that product still has a market outlet and what the best methods are to manufacture it using the least amount of resources possible.
5. Improving customer service
We cannot overlook the importance of customer service in a company. Many companies have spectacular products and design, but if they have poor customer service sooner or later it will all go down the drain.
With lean management you will deliver the product in the shortest possible time and just where and when the customer wants it. You will see the change from the beginning, so it's time to apply it in your company.

Lean management guidelines
In order to apply lean management properly, it's important to follow a set of guidelines so that all changes achieve the objectives you set out at the beginning of the whole process.
1. Defining value from the customer's perspective
At the beginning of this article we mentioned that the objective of lean management is to continuously improve in order to optimise the processes that generate value for the company. Now, what is value?
We define value as anything that solves a customer need, so your focus should be on simplifying processes that adequately serve your target audience.
All the changes you implement must be oriented to attend to the customer and build customer loyalty in order to obtain medium and long term profits. Therefore, any process that doesn't do this should be discarded.
2. Eliminate steps that do not generate value
Closely related to the previous point, only that in addition to focusing on improving the processes that add value, you will eliminate at the root the steps that are not oriented to the customer's needs.
It's important for your team to analyse the company's situation. Sometimes just by looking at the organisational structure, you will realise that there is something wrong, and that there are many positions and lines of command that are simply unnecessary.
So now you know, if you see processes, tasks and personnel that do not seek to service the customer, you will have to eliminate them in order to improve results in the medium and long term.
3. Organised sequence
There's nothing worse than seeing a messy company where everyone does what he or she wants or where there's no precise order in which tasks are done.
Any organisation that does something similar is destined to fail sooner rather than later.
The good news is that with lean management you will have an ace up your sleeve to transform all the problems the company has at the root. Forget the clutter and create standardised processes in all areas of your company.
4. Repeat the first three steps to eliminate waste.
The last guideline of lean management is that you must repeat the first three steps to eliminate all the waste that was not deleted at the first attempt.
This is done with analysis and more analysis, so take as much time as necessary to make a total change in the organisation.
Leaders' activities in lean management implementation
One of the keys to lean management is that everyone in the organisation must be committed to making the relevant changes to take the business to the next level.
Leadership positions have a critical role to play in this process. Let us look at some of the tasks they must perform to ensure success.
1. Aligning with the company's objectives
First of all, leaders must be 100% aligned with the objectives. Remember that the leader is the mould in which the other copies will be made, so if you want something to happen, you must be the first to do it.
Focus on showing the objectives of the project and motivate everyone to set their sights on them. In a short time you will see how everything starts to take shape.
2. Mobilising the organisation
By mobilising the organisation we mean supervising that the necessary changes are being made. This is very useful in companies that are very large and have a lot of staff.
It will be tedious at first, but as the days go by you will see that resistance will drop significantly.
3. Accelerating cultural change
Last but not least, the leader has to accelerate cultural change.
This is the most complex step, as cultural change takes time because of the many years of working in a different way. It's important to talk about the benefits that everyone will gain from this new method.
The truth is that lean management is one of the most important organisational trends today. All companies should apply it if they want to be competitive in a world where there are more and more predators.
Do you want to remove the many barriers you have in your business?
Decide to implement lean management and you will see how the results will surprise you!
Let us know in comments what your impression of lean management has been, would you be willing to implement it in your business?
Looking for something specific?