Value Stream Mapping (VSM): what is it and how to do it?
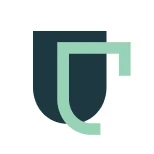
Franco Brutti
Value stream mapping is one of the tools of the Lean Manufacturing methodology, and one of the most powerful techniques for business growth.
This technique has a huge range of applications in all kinds of industries, from manufacturing and logistics to software development. And if you’re looking to create or strengthen your workflows, this is one of the best tools to achieve it.
For this reason, we will explain what VSM is, its different types and when and how you can apply this method. In addition, we will give you some of our best tips to put it into practice and improve your value streams.
What is value stream mapping?
Value stream mapping is a visual tool. In other words, a map.
A map to illustrate workflows, organizational processes and business strategies.
A map used in Lean Manufacturing and Lean Management to identify and eliminate "waste". That is, all those activities that do not add any value to the work process.
This map is an invaluable resource when it comes to optimizing workflows at all levels. And although it was devised to perfect production lines, it can be applied in countless industrial and business contexts.
This map can illustrate work processes in great detail from start to finish. And when we say "fine detail," we mean everything from the stages of each process to the activities, decisions, people and materials involved, among many other elements.
The best part: you can use the map to thoroughly analyze your current processes, but also to develop future value streams. Flows where you have refined your current processes and eliminated their flaws and weaknesses.
Now, to better understand how to map value streams and how to create a high-caliber VSM, we need to understand the concept of value stream and its parent methodology: the Lean methodology.
The Lean methodology
The Lean methodology is one of the preferred agile methodologies for production process improvement and business management.
This philosophy was born in the Toyota production system in the 1970s, thanks to engineers Taiichi Ohno, Eiyy Toyoda and Shigeo Shingo. Since then, it has become the basis for countless industrial and business strategies around the world.
The objectives of this philosophy are:
Maximizing the value of business processes.
Minimizing waste in workflows.
Ensuring high quality products and services through much more efficient processes.
In other words, to achieve the best results with the minimum possible resources.
Of course, we are talking about financial resources, time, effort, space, machinery, materials and human resources?...
Now, let's take a look at its key concepts:
Value: any activity, process or characteristic of a product or service that is valuable to the customer. In other words, everything that represents tangible benefits for the customer, emphasizing what the customer is looking for and what he needs.
Waste: anything that doesn’t add value at all to the final product or service. For example, unnecessary waiting times, overproduction, repetitive checks, redundant or unnecessary procedures and defects.
Value stream: the complete end-to-end process, including all activities, communication channels, materials and so on to deliver the final product or service.
Continuous improvement: the Lean philosophy is based on constant review of work processes, as well as analysis and continuous improvement. This is where the value stream map becomes an essential factor in putting this methodology into practice.
The 3 phases of the VSM
This map can be applied in the following versions. Each of these versions can be applied on its own. However, if you want a total view of your work processes and how to improve them, it’s best to work with all of them.
These versions are:
Hypothetical value stream mapping: perfect for making an initial sketch of the work process. However, for many, this VSM is optional. To obtain it, the parties involved have to have an initial notion of the current processes.
Current value stream mapping: this has to represent the current process as accurately as possible.
Future or ideal state value stream mapping: this will illustrate the goals of the implemented VSM. In other words, the workflow already optimized and without waste that could delay, hinder or obstruct the production line.
However, remember that Lean methodology and value stream mapping are based on continuous improvement. The margin of error is inevitable; therefore, this process must be repeated constantly to minimize the margins of error in the value streams.
When to use VSM?
Value stream mapping has a huge range of applications. For example, you can use it when it comes to:
Improving a current work process as a whole.
Identifying bottlenecks within the production line.
Reducing production, logistics and transportation costs.
Reducing lead times and workloads.
Analyzing your current processes in depth and understanding their complexity.
Communicating your business strategies to customers, teams and stakeholders.
Finding optimization opportunities.

Where to implement this method?
You can implement VSM in a myriad of scenarios. However, these are the most common and profitable ones to implement it in:
Production: this approach was devised to optimize production and distribution lines, so it's a perfect fit for manufacturing and supply chain - no matter the product or industry.
Digital product development: perfect for organizing remote workflows, organizing schedules, delegating tasks and accelerating the entire software development, testing and optimization process.
Logistics: this map can also help you to find faults in transportation lines, waiting and moving times, and product delivery.
How to create a value stream map
This is the step-by-step guide to implement value stream mapping from scratch:
1. Know and define the process to be mapped
First and foremost is to establish the boundaries of the process you want to map and make it clear and explicit.
This is where you have to define the starting point and the end point of the value stream. And of course, the process or workflow you want to analyze. In turn, the products, services and operations to be studied.
This will also help you to keep your or your customer's business objectives, practical applications and priorities on sight.
2. Identify everyone involved
In other words, all the tasks and people involved in the value stream.
Collaboration, communication and coordination between teams are essential parts of the VSM, and are also part of the ultimate goal. Therefore, it’s fundamental to know:
What the teams and members involved will be.
What the tasks of each member will be.
What the communication channels will be.
Where the stakeholders are involved.
In this way, you can detect:
How many people are within the value stream.
What tasks are still to be delegated.
Who has many or few responsibilities.
Who is involved with other teams.
Who is doing tasks that do not correspond to them.
For many it may seem unnecessary, but in many cases, many members do not know who does what. Also, in many cases, not all members know each other directly, especially if we are talking about remote teams.
This scheme alone will help you avoid communication problems among participants and management problems when delegating.
3. Value Stream Mapping of your current map
Time to start defining the value stream in its current state.
The process has to be as accurate, precise and reliable as possible, with all the details, insights and highlights you can possibly include. Remember that this will be your basis for your optimization strategies and future scenarios.
Now, to ensure the effectiveness of your map, it needs the following metrics:
Time taken for each operation, or value-added time.
Total cycle time.
Waiting times.
Resources required for each task.
Number of people needed for each operation.
Tools required for each task.
Workload.
Transportation and delivery times.
4. Create an analysis of the current process
This is where you take all of the above metrics to measure, analyze, compare and contrast them.
At this point, you will get a total picture of your entire workflow operation, as well as its strengths and weaknesses and their causes.
This is where you can determine what areas you can improve within your work process, what are the priorities and what are the wastes to be eliminated.
5. Create a value stream map for the future state
Time to design a VSM that is more efficient, more effective, and better aligned to business objectives.
At this point, you can directly attack the weak points of your current flow and design management strategies to eliminate them.
And if we talk about time, you can also use Takt Time or tactical time. This term refers to the speed required to complete the tasks in your workflow and meet the demands of the customer or your company.
This way, you can focus entirely on production, task completion, transportation and delivery times and reduce the times as much as possible. And in this way, you can improve the productivity of your workflow and your bottom line.
6. Implement your action plan
And now for the best part.
It's time to take your new action plan and turn your strategies into tangible results.
Your plan also needs to have implementation dates. And in turn, a follow-up plan to track and monitor the performance of the workflow and its different variables.
And most importantly, constantly test the effectiveness of your new value stream, adjust where necessary and record absolutely everything. This way, you will not only develop more effective plans, but you will have a solid knowledge base for future strategies.

Tips for putting value stream mapping into practice
Before we finished, we thought some additional tips would come in handy in practice.
Define the company's goals and objectives: because it’s so easy to lose sight of your customer or business priorities and focus too much on the process. Make sure your VSM aligns with your objectives at every stage, without exception.
Thoroughly analyze existing processes: for your value map to be accurate, analyses need to be as thorough as possible. Be sure to record every task, every step, every tool, facet and variable before you start mapping your strategy.
Start at the end: this way, you will be able to focus first-hand on the priorities and activities involved. In addition, you will have a more fluid and direct communication with customers, leaders and stakeholders and avoid loose ends in your strategy.
Integrate the right team: because every strategy is only as efficient, effective and functional as the team that carries it out. In turn, make sure that all participants know the value stream map and their role within the overall strategy.
Let's get to work
You now have everything you need to adapt this approach to your different value streams and work processes.
Remember, this method is perfect for both production lines and digital product development. But you can also use it to refine your services and those of your customers.
Don't forget to constantly refine your value stream maps to detect potential flaws and minimize margins of error whenever possible.
And now it's your turn. What ideas can you come up with to put this approach into practice? Do you know of other methodologies for business management? We'd love to hear your perspectives and highlights in the comments.
Looking for something specific?
16 feb 2024
12 dic 2023
1 dic 2023
20 nov 2023
17 nov 2023
12 sept 2023